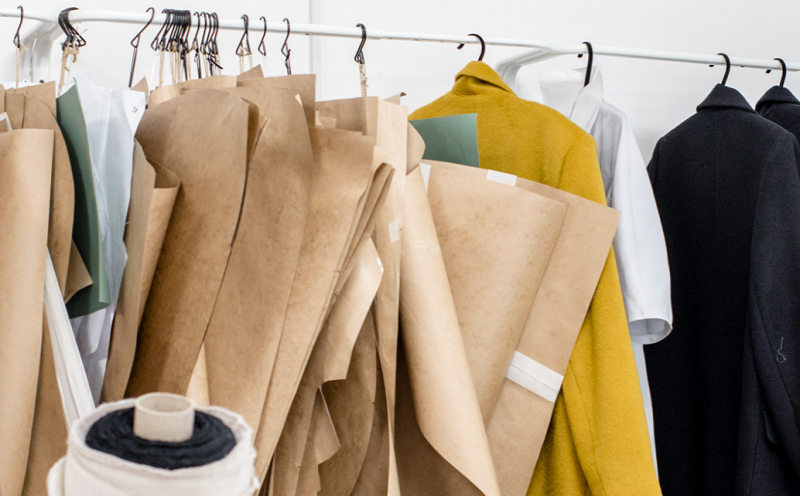
When we talk about garment manufacturing, we mostly cover bulk production processes. To know about the complete garment manufacturing process one should also learn about the pre-production process.
What is a pre-production process? The processes that are done prior to the start of bulk garment production are known as pre-production process. From sample development, approvals, research and development work for orders, testing of raw material to pre-production meeting are pre-production process. Pre-production processes are very important for the efficient production.
A typical garment export house generally has following pre-production processes:
1. Meeting with buyers
In this stage, the designer of a manufacturing house shows their creations, latest designs to buyers. On the other hand, if the buyer already had fixed design of a style and need few changes on it related to fit, fabrics or trims they discuss those things with the merchandiser of the manufacturing unit.2. Development of initial samples for the buyer
In this stage after receiving buyer’s concept or instructions on the new style, samples are made with available fabrics and trims. Sample development is carried out by sampling team under supervision of sampling merchandiser. If needed, new development requirement from raw fabrics, trim and garment samples are discussed with buyer.Often buying houses closely follow up the new sample development.
3. Development of fabric sample, bit loom, print and embroidery artwork
The fabric is developed as per the buyer requirement. Fabric development means sourcing of customer specific fabric with matching properties, dyed and finished for solid colors. For the solid color lap dip approval is a very important process. Until lap dip sample is approved merchants re-submit lap dips. In case of yarn dyed fabrics merchants develop fabric sample with specified design, stripes or checks. These fabric samples called as Bit Loom. Other approvals such as print and embroidery artwork approval and color approval are done. It may be done a later stage at the time of pre-production.4. Costing of a garment (complete cost as well as manufacturing cost)
Merchants prepare cost sheet with details cost break up such as raw material cost, manufacturing cost, overheads and margin. Costing is very a critical stage. Because whether a company will get order or not depends on their costing. If the garment cost is very high then the manufacturer may lose the order and on the other hand, if the factory keeps their cost low, they will not earn profit from the order. Estimation of the garment cost should be done on data based.5. Pattern making, correction of pattern, pattern grading
In a factory, a pattern master prepares the first fit pattern. Then re-develop pattern adding buyer comments and rectification on a fit sample. After fit approval, pattern master grade pattern for size set samples only for specified sizes.Once the order is ready for production they grade patterns for whole size range. For pattern making garment factories normally use CAD system in additional to the manual pattern drafting and pattern grading.
6. Fit sample, size set sample making and approval from buyer
Each sample has a certain purpose. Samples are made in the sampling department and the physical samples are sent to the buyer for approvals. Designed and concerned merchandiser form buyer's end review the garment samples against the design and tech pack and provide their comments on the submitted samples.Know more various types of garment samples.
7. Correction of fit samples according to buyer comments
If the sample is not approved or further work is recommended by the buyer. Correction is done and re-submitted to the buyer.8. Sample approval process
In this stage sample approval is taken from the buyer. Approval of fabric swatches, print colors, embroidery design, beadworks and other processes are covered. Sometimes factory=ies need to take approval of trim cards as well.
9. Production planning, Material planning and line planning
To start production on time and ship the order on time planning is a must. Planning is needed for material sourcing, production capacity, line planning. Scheduling of jobs and responsibility is defined at this stage.10. Placing an order for fabrics, trims, accessories and packing materials
Sourcing of raw material. Raw materials include fabrics, all kind of trims and accessories.11. Testing of fabrics and other raw materials
Physical properties are being tested for bulk fabric. This test can be done in in-house testing labs.12. Study of approved sample
For operation breakdown, calculating work content, identifying critical operation and line setting technical team and industrial engineers study the approved garment sample.Also finding the best ways for producing the garment most efficiently in the production stage.
13. Pre-production meeting
Once pre-production (PP) sample is approved (also called sealer sample) and most of the trims are sourced, merchants or production planning department conduct pre-production meeting with the production team, quality team and sourcing team. All important comments, procedures to be followed, dos and don’ts are discussed.Scheduling of PCD (planned cut date) and shipment date is announced to all teams.