This article is contributed by Nisha Sah.
In this article, Nisha has explained the process for synchronizing the cutting department using a Kanban dashboard. The process is also known as the cut priority system.
Important Terms in Kanban System
The Kanban system is a workflow management and control technique that is particularly useful in manufacturing. Numerous organizations all over the world have embraced Kanban because of its ease of use and ability to boost output and efficiency.
A Kanban dashboard is a visual tool that helps manage work by displaying tasks and their status. A visual board that is frequently divided into columns to depict the various workflow stages is the central component of the Kanban system. One might designate a distinct production stage for each column, for example, "To Do," "In Progress," and "Done”.
Cards, also known as Kanban cards, are used to represent work items and are moved across the board as they move through the process. Usually, these cards provide details regarding the assignment, like its description, and its importance.
Reducing the quantity of work in progress (WIP) at every level of the workflow is one of the fundamental tenets of the Kanban methodology. This keeps teams and individuals from being overworked and guarantees that the system processes run efficiently. The maximum number of jobs permitted in each stage at any one moment is indicated by the WIP limits that are specified for each column on the board.
Work is only pulled into the system when there is enough capacity to handle it, which is how the pull system of Kanban works. By doing this, bottlenecks are avoided and resources aren't squandered on projects that take time to finish.
Kanban promotes continual improvement by routinely analyzing and streamlining the workflow. Teams frequently convene on a regular basis, referred to as "Kanban cadences," to review system performance, pinpoint areas for development, and make necessary modifications.
Kanban encourages transparency and makes it easier for teams to spot inefficiencies and areas for improvement by giving a visual depiction of the workflow and the status of each job.
For the cutting process, it will involve tracking different stages of cutting orders and prioritizing them based on certain criteria. It takes several steps to create a garment cutting priority table Kanban dashboard. Here's a guide to setting up such a dashboard:
Steps to Create a Cutting Priority System
1. Identify the Key Stages in the Garment Cutting Process:
- Fabric status- Fabric Status is the first step of production where the fabric is allocated to cutting for further process. Fabric store team had been assigned a line plan according to which the fabric had been allocated to cutting and when the allocation is raised by cutting the first Kanban card is raised.
- Layering & Cutting- Layering and Cutting is the initial steps after the fabric is being received; firstly the layering is being done followed by cutting.
- Stickering- After layering and cutting kanban card is move to stickering. In this step all the cut panels are stickered with a number. This is an important step it helps in mismatch cases amongst bundles and also acts as a barrier for color variation defect.
- Fusing- After Stickering Kanban card moves to Fusing, it is the step where needed parts are being fused to provide additional strength during garment construction.
- Bundling- After fusing Kanban card moves to bundling all the parts are brought together in bundling section and all the bundles are made according to serial wise and bundle numbers are been allocated.
- Input to Line- After bundling kanban card moves to issue to line which depicts a clear indication for the sewing team to collect the bundles and feed the sewing line for production.
2. Determine Information Criteria:
- Style Name- which style order is being raised that style name.
- Color-same styles must have different colors that are also mentioned.
- Order number- a specific order number is being allocated to every order that is also mentioned.
3. Choose a Kanban Tool:
- Display board- A display board where different columns are been made for different stages of cutting.
- Visual cards- small cards which is also known as Kanban card which will move from one stage column to another.
4. Set Up the Kanban Board:
Columns: Each column represents a stage in the process.
- Fabric status
- Layering & Cutting
- Stickering,
- Fusing
- Bundling
- Input to Line
Cards: Each card represents an individual order.
Add Details to Cards:
- Style Name
- Color
- Order number
5. Track Progress:
- Move cards across columns as the order progresses through each stage.
- Ensure that high-priority orders are moved and addressed first.
6. Review and Adjust Regularly:
- Regularly review the dashboard to ensure priorities are being met.
- Adjust priorities as needed based on changes in order requirements or new incoming orders.
Example Kanban Dashboard Setup
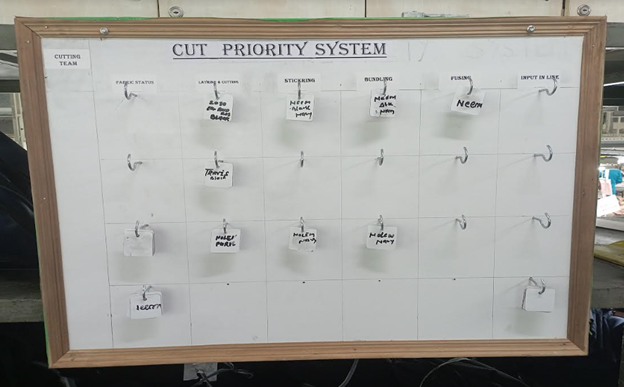
Fig – 1: Cut Priority Board
Operating procedure of the cutting department:
- The orders of cutting requirements will be shared with the cutting team.
- The Kanban card is filled with details which include order number, color, and style name.
- Kanban card is placed in the cut priority system board, in the first row that is Fabric Status which shows that it is a new order and its fabric request has been sent to the fabric store.
- When the fabric arrives and laying starts, the Kanban card is shifted to the next row which is fabric layering and cutting.
- When fabric layering is done followed by cutting the card moves one step ahead and placed at stickering.
- After allocating each cut panel a definite numbering through stickers the card is moved to Fusing.
- After fusing is completed at some panels, all the cut panels are sent to the bundling section where bundles are created.
- After completing the bundling process, the kanban cards are moved to the final step of issuing to the line. This indicates that cutting is ready and it can be collected by the sewing team and henceforth the process proceeds to sewing.
How to Sustain the Process?
- After every task one allocated person will come and move the cards accordingly.
- Supervisors and responsible persons of the cutting department will take responsibility for the board updating and card movements.
Related Article: Functions of Cutting Department in Garment Industry
Benefits of Using a Kanban Dashboard for Garment Cutting:
Visual Management:
Easily see the status of all orders at a glance. Kanban boards offer a clear visual depiction of the state of the work, making it simple for all departments involved to know what has been finished, what needs to be done, and what is currently being worked on. Team members' communication and collaboration improve as a result of this transparency.
Improved Workflow:
Workflow becomes more predictable and fluid with Kanban. This guarantees that work is started promptly when needed, cutting down on waiting times and idle resources, which results in shorter lead times in the cutting process. Smooth transition between stages reduces bottlenecks.
Fig – 2: Benefits of the Kanban System
Enhanced Communication:
Clear priorities help teams understand what to focus on. Employee empowerment comes from giving them greater control and ownership over their work through the use of Kanban. Having team members manage their own work queues can boost engagement and motivation. Furthermore, because team members might need to step in to assist with tasks outside of their regular responsibilities, Kanban encourages cross-training and skill development.
Flexibility:
Kanban facilitates adaptability to shifts in priorities or demand. The Kanban system helps the team to swiftly modify their workflow and prioritize tasks without causing any disruptions.
Using a Kanban dashboard for cutting prioritization can greatly enhance efficiency and ensure that high-priority orders are processed on time, leading to improved customer satisfaction and better management of resources. Kanban facilitates a culture of continuous improvement by encouraging routine workflow reflection and the discovery of optimization opportunities. Teams can find areas for improvement, inefficiencies, and bottlenecks through regular retrospectives and daily stand-up meetings. This allows for continuous improvements to be made to the cutting process.