This article is written by Susmita Sarkar.
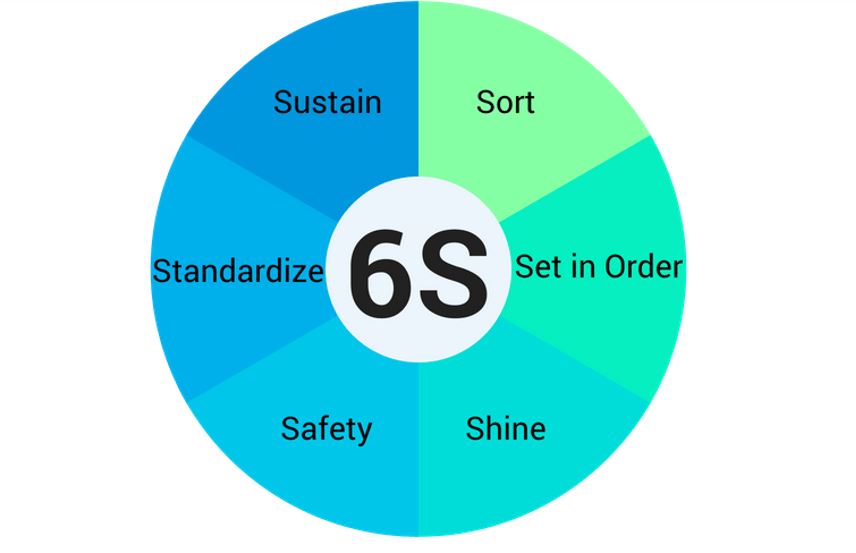
The criteria for a quality management system are no longer the only thing that manufacturing organizations need. It also demands ongoing improvements in the management of quality and the safety of plant employees. With the support of numerous cutting-edge techniques and procedures, this necessity is fulfilled in the manufacturing industries.
To meet the needs of manufacturing enterprises, 6S is one of the most widely used methodologies today.
In this post, Susmita has explained the 6S methodology. Later she has shared a list of benefits of implementing 6S in workplaces.
The original Japanese terms for 5S are:
After that these were translated into English with the addition of safety:
To meet the needs of manufacturing enterprises, 6S is one of the most widely used methodologies today.
Introduction
The 6S method is the more upgraded version of the 5S approach. The 6S approach is a way of organizing and managing a workplace that is well-kept, efficient, high-quality, and safe for employees in any firm. The 5S method originated in Japan. It was developed by Hiroyuki Hirano, and 5S was first used by Toyota in 1970.In this post, Susmita has explained the 6S methodology. Later she has shared a list of benefits of implementing 6S in workplaces.
The original Japanese terms for 5S are:
- Seiri
- Seiton
- Seiso
- Seiketsu
- Shitsuke
After that these were translated into English with the addition of safety:
- Sort
- Set in Order
- Shine
- Standardize
- Sustain
- Safety
6S Methodology:
S1: Sort
The goal of Sort is to distinguish between objects that are required for work and objects which are not required for work. The workspace should be cleared of any items that are no longer required or in use. Some may be completely trashed, some may be placed nearby for convenient retrieval, while others may be Red Tagged (Figure-1) and placed in a disposition area for further review. It keeps the workplace clean and efficient for receiving and searching for items and reduces the duration of the operation.

Fig -1: Red Tag (Used for sorting items)
Fig -1: Red Tag (Used for sorting items)
S2: Set in order
Set in order means managing all the items in a proper way and place at the workplace for quicker access and use. Make sure goods can be identified by appropriately tagging them. Every working approach has a unique kind of order. Determine it, then fix it.
S3: Shine
Regular cleaning keeps the office tidy and clean. Cleaning practices are observed when using cleaning equipment, a workshop, and a light source. Operators should be mindful of their own cleanliness and maintenance.
S4: Standardize
Standards should be developed and implemented in the workshop. In order to keep the workplace tidy and organized, management should provide employees with clear instructions. Participation from all workplace employees is required for this activity. It aims to help people in creating consistent work processes and form more productive habits. This can be achieved by giving visual reminders, defining workers’ responsibilities, and conducting routine inspections and site checks on a regular basis.
S5: Sustain
The main objective of sustaining is to set up a clean environment, and keep it that way permanently. This raises employee awareness and improves quality. Additionally, it improves worker relations and communication.
S6: Safety
The main step of the 6’S method is safety. Safety involves a number of regulations and safeguards to shield employees from workplace accidents. For this safety equipment is also used like safety helmets, safety gloves, fire extinguishers, etc. Ensure that all necessary safety supplies, such as first aid kits, personal protective equipment, and fire extinguishers, are available at the workplace. All safety equipment should be regularly maintained in the workplace.
Adding Safety helps provide further focus on safety issues, and the extra attention can help to ensure that no hazardous chemicals or components are overlooked after going through the stages of 6S
Additionally, workers should put on the proper personal protective equipment (PPE) to protect themselves against risks that are difficult to control or cannot be eliminated. Such as, in the cutting department (apparel industry), when the operator is cutting the fabrics using a straight knife and band knife, he/she should wear metal mesh gloves (Figure-2) for their safety.
All employees must get training and be informed of various safety procedures, including the proper use of PPE, through meetings and training.

Fig-2: Metal mesh gloves
Also read: 10 Steps for effective implementation of 5S
References
Anon., n.d. Google. https://liveroomlk.medium.com/lean-6s-management-system
Dhounchak, D., 2017. Review of 6S Methodology. IJDR, 07(2017).
Why was safety included in 5S?
We are aware that every workplace puts high importance on safety. Having a clean and safe workplace is important because:- It encourages a stress-free, healthy environment where employees may feel safe and secure
- It improve productivity and quality
- It makes it simple to identify possible dangers and implement safety controls.
Adding Safety helps provide further focus on safety issues, and the extra attention can help to ensure that no hazardous chemicals or components are overlooked after going through the stages of 6S
Various Techniques for Completing the Safety Step:
The first step in ensuring safety is identifying potential threats as well as those that already exist. Each employee is required to be knowledgeable about the various work-related risks and to assess these risks using job safety analyses (JSA) or risk assessments.Additionally, workers should put on the proper personal protective equipment (PPE) to protect themselves against risks that are difficult to control or cannot be eliminated. Such as, in the cutting department (apparel industry), when the operator is cutting the fabrics using a straight knife and band knife, he/she should wear metal mesh gloves (Figure-2) for their safety.
All employees must get training and be informed of various safety procedures, including the proper use of PPE, through meetings and training.
Fig-2: Metal mesh gloves
Also read: 10 Steps for effective implementation of 5S
Benefits of using 6S in the workplace:
- A decrease in the price of material handling
- Workplace became neat and clean
- Any kind of tools or instruments can be easily accessed
- Important files can be easily accessed
- Saves process time
- Always neat and clean equipment present in the workplace
- All things are in an organized manner
- Increase productivity of the plant
- It increases the quality of products
- Reduce the risk of worker injuries
- Boost internal communication among the staff
- Create a safe environment for the workers in the industry
- Reduce manufacturing cost
- Improves workplace safety
- Increase the speed of the work in the workplace
- Reduces wastage in the plant
- Reduces the risk of workplace tool and equipment failures
- Increase the overall efficiency of the workplace
Conclusion
After studying the 6S method, we can say that it is incredibly advantageous to any organization or manufacturing industry. The main objective to implement this method in the industry is to get rid of excess inventory, enhance process flow, organize work, provide a safe working environment, and make the work atmosphere healthier. Any organization's overall performance is improved through the 6S method.References
Anon., n.d. Google. https://liveroomlk.medium.com/lean-6s-management-system
Dhounchak, D., 2017. Review of 6S Methodology. IJDR, 07(2017).
About the Author:
Susmita Sarkar is pursuing a master degree in Fashion Technology at National Institute of Fashion Technology, New Delhi, India. She has completed her B. Tech in Apparel Production and Management from GCETT, Serampore.