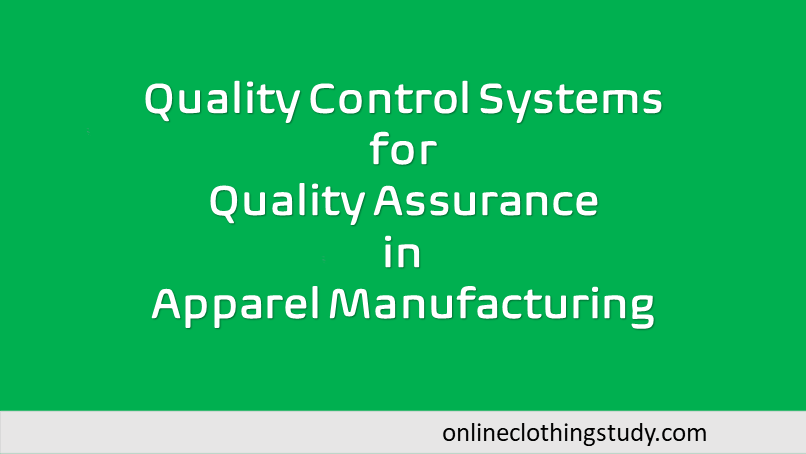
In the last article, I covered the topic - How to set control systems to assure raw material quality in garment manufacturing. To be one of the best in quality garment manufacturing, we have to be more aggressive in setting control systems of production processes.
But we have seen many factories fail after setting control systems. It is because failing to monitor the systems and processes on a regular basis results in rejections and rework.
Constant monitoring of the systems is necessary to ensure that fulfilling their purpose. So in this article, we will discuss various control systems and ways to monitor the production process on a regular basis.
Following are some of the control systems which needs to be implemented to ensure the correct quality of cut parts:
- Quality control in the cutting process
- Quality control in printing and embroidery process (outsourced processes)
- Quality control in the stitching process
- Quality control in the washing/Dyeing process
- Quality control in the finishing section
1. Quality control in the cutting process
Cutting is the most critical area which needs to be closely monitored. If one wrong cutting happens, the rejection quantity will be huge. This department also deals with the most important raw material i.e. Fabric which holds the largest value of the cost. So we can’t just afford to waste fabric by wrong cutting.Following are some of the control systems which needs to be implemented to ensure the correct quality of cut parts:
Layer checking:
Lay length and lay height need to be checked for every lay and must be recorded by the quality checker. Lay length should not be less than the marker length and lay height standard which many factories follow is 3 inches. This report should be monitored by the cutting in-charge and the quality supervisor of the cutting section on daily basis.
Marker checking:
Marker should be checked for length, number of cut parts, pattern, and grain line. Every new marker should be checked by the quality checker and the record must be kept the same which should be monitored by cutting in-charge and quality supervisor on a daily basis.
Fused part checking:
This is an important area that is generally missed by many factories. The bonding strength of fused parts must be checked randomly at least twice a day. Also, machine parameters like temperature, pressure, and speed must be checked against required parameters after every two hours and data must be recorded.
Cut Parts Checking:
Cut parts should be checked layer-wise with patterns for shape, notches, and drill marking. Checkers should maintain a report of the same and this report should be checked by the quality supervisor on a daily basis.
Panel checking:
Panel checking is necessary to segregate defective panels and replace them so as to reduce final garment rejection due to fabric defects. But all factories do not follow this process.
Some factories proceed with checking of big parts only. It depends on the type of garment you are producing. If you are making high-end garments in short quantities then this process is a must otherwise there will be a huge rejection and rework at the finishing stage.
It is up to the factory to adopt this process as per their requirement. If you are following this process then a report must be made and analyzed monthly by the cutting and quality manager to monitor the percentage of defective panels as it involves re-cutting of fabric which involves cost.
If the quantity of defective panels is high then we have to check whether our process of 4-point inspection is followed properly or not.
Also to ensure no shade variation in the cut panels. It is necessary to maintain the report of re-cutting with panel number and roll number which is used for re-cutting.
Audit:
This is a random audit of ready-to-issue bundles for numbering, shade, pattern, bundling errors. This can be done by a quality supervisor and the report must be maintained and checked by the quality manager monthly.
2. Embroidery/ Printing
If there is any process of embroidery or printing on cut panels then 100% of panels must be checked and reports should be maintained on a daily basis. Embroidery and printing quality should be checked by the quality and production supervisor. It will help in eliminating any major causes of defects if any.3. Quality control in the stitching process
Sewing section in the heart of a garment factory. It involves the conversion of cut panels into ready garments as per customer requirements. This area is very much labor intensive with less or mild use of technology or automation.It is so dynamic in nature that everyone should be on their toes otherwise chances of rework will increase. Production and quality person's involvement is very much critical to the process. The correct method, machine setting, and quality standards must be followed to reduce rework and increase efficiency.
Following are some of the control systems which needs to be implemented to ensure the correct quality of the product:
Following are some of the control systems which needs to be implemented to ensure the correct quality of the product:
Parts checking:
Audit is required by the quality supervisor to ensure the quality of the output. All the parts must be audited hourly and a report should be made and reviewed by the sewing and quality in-charge on daily basis. A practice of self-checking must be incorporated in sewing operators so as to ensure quality at the needlepoint.
Inline checkpoint:
There should be at least one inline checkpoint in the sewing line. This can be placed at the most critical operation which is most prone to defects. Quality in-charge along with production in-charge can decide at which operation this checkpoint must be kept. At this checkpoint, 100% of garments should be checked and a report should be maintained.
Final checkpoint:
Final checkpoint:
This is the most important checkpoint for a sewing line. 100% garments should be checked at the final stage and defective ones should be returned back for rework. The report needs to be maintained of DHU and should be analyzed by quality and sewing floor in-charge on daily basis. This report should contain no. garments checked, passed, defected, name of defect, and name of the operation.
Quality Audit:
Quality Audit:
All the passed garments should be audited on AQL basis before proceeding for finishing. The AQL level can be set as per buyer requirements. Generally, many factories follow 2.5 AQL. Lots which passes should be sent for finishing. Rejected lots must be checked again. In an audit, we must check the garments with approved samples for construction, measurements, trims, and workmanship. If possible the audit must be done for each checker so that we can identify which checker is making more mistakes while checking. A report must be made on daily basis for audit and should be monitored by the quality head.
4. Quality control in washing, dyeing, and printing process
In case of any other process like washing/ dyeing or printing then 100% of garments should be checked for open seams and measurements.A quality inspection report should be maintained and checked by the quality and production supervisor on a daily basis.
Final checkpoint:
5. Quality control in the finishing department
This is the most critical area of a garment factory. The workload in this section will always be high. So to ensure quality in finishing is not an easy task. Following control measures can be implemented to maintain the required level of product quality:Final checkpoint:
100% of garments are checked for pressing, stains, and other visual defects. This is the last checkpoint of the process. Reports should be made and should be monitored on a daily basis by finishing and quality incharge. After checking measurement must be done to ensure nothing is out of tolerance.
Polypack checkpoint:
Polypack checkpoint:
After poly packing, all the garments are checked for packing presentation. Also, barcodes, packing trims, and price stickers are checked to ensure everything is ok. A report should be maintained for the same.
Quality audit:
Quality audit:
As we audit in the sewing section, the same must be done here also. The AQL level can be set as per buyer requirements.
Pass lots can be sent for the carton packing. This audit must be done in the same way as our customer does the final inspection.
A report must be made on a daily basis for audit and should be monitored by a quality head. This report also serves as the factory's internal inspection report which is required by many customers.
Carton Audit:
Carton Audit:
After all garments are packed and the packing list is generated, 100% of the cartons audit is done for correct packing. The auditor must tape the carton after the audit so that no one could access the carton again without permission. This will ensure that we don't get any shortage complaints about the shipment. Reports should be maintained for the same and must be monitored by the quality heads daily.
Following the above control measures and a detailed analysis of the reports will highlight the root causes of the problem. It will help to solve the issues and will ensure 100% FTR.
Following the above control measures and a detailed analysis of the reports will highlight the root causes of the problem. It will help to solve the issues and will ensure 100% FTR.