Among the many fashion and apparel products, denim jeans and other denim products have a separate identity. When it comes to the discussion of sustainability in the fashion supply chain, the first product that comes into our discussion, is denim manufacturing. Many apparel brands have already taken various initiatives to make denim jeans production more sustainable.
Online Clothing Study (OCS) team has done some research on the sustainability work done by brands and organizations. Further, a little note has been added on what action can help us reduce the impact and make the denim manufacturing process more sustainable.
According to Statista, a market research company, the global denim jeans market will generate around 129.8 billion U.S. dollars in retail sales by 2021, up from 100 billion U.S. dollars in 2016. The denim jeans market is a sub-category within the overall apparel market. As the global apparel market grows, it is unsurprising that the denim jeans market will also rise. Jeans are stable apparel products and are considered the most comfortable clothing.
Statista has also shared - Denim, a fundamental component of the casual wardrobe, has become a staple textile within the global apparel market. The market value for denim fabric was 90 billion U.S. dollars in 2019 and was expected to increase to 105 billion U.S. dollars by 2023. Denim or blue jeans are by far the most valuable product in the denim industry, though there has been an increase in value for every type of denim clothing item.
According to Statista, a market research company, the global denim jeans market will generate around 129.8 billion U.S. dollars in retail sales by 2021, up from 100 billion U.S. dollars in 2016. The denim jeans market is a sub-category within the overall apparel market. As the global apparel market grows, it is unsurprising that the denim jeans market will also rise. Jeans are stable apparel products and are considered the most comfortable clothing.
Statista has also shared - Denim, a fundamental component of the casual wardrobe, has become a staple textile within the global apparel market. The market value for denim fabric was 90 billion U.S. dollars in 2019 and was expected to increase to 105 billion U.S. dollars by 2023. Denim or blue jeans are by far the most valuable product in the denim industry, though there has been an increase in value for every type of denim clothing item.
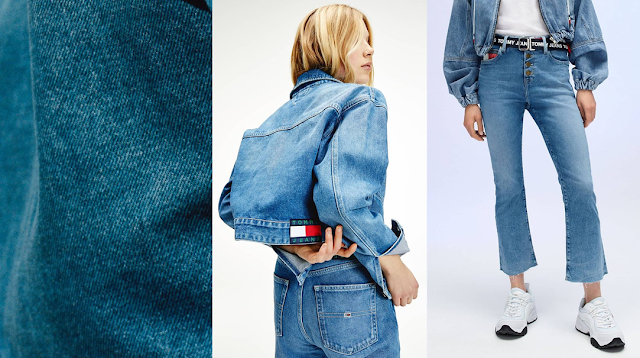
Image credit: nl.tommy.com
Although the denim business is flourishing gradually, nowadays, it has seen some problem due to some environmental issues created by it. Very often it comes to news that labour or workers has faced tuberculosis or silicosis due to corrosive effect of sand blasting which not only worn out the skin but also create breathing problems due to harmful gases. Washing and chemical processing of cotton fabrics in denim manufacturing is one of the main causes of rise of concern for environmentalists.
Sustainable ways are being figured out nowadays in denim manufacturing in countries like India and china.

Sustainable ways are being figured out nowadays in denim manufacturing in countries like India and china.
Growth of eco-denim/environment-friendly denim

Source: https://edited.com/resources/denim-trends/
Making jeans in a more sustainable way
All the stake holders of the denim fabric and jeans supply chain are aware about the importance of producing denim in a sustainable way. All brands know why they should take care of the environment through acting best practices.
1. Use of Organic cotton Increased:
1. Use of Organic cotton Increased:
Organic cotton is grown usually using methods and materials that have a low impact on the environment. It maintains soil fertility, reduce the use of toxic and pesticides, fertilizers, and helps to build biologically diverse agriculture.
Nowadays 100% organic cotton are being used without even bleaching of that cotton fabric where environment friendly enzyme finish and dry techniques are been used.
2. Dry techniques of denim manufacturing:
The dry technique of denim manufacturing is the process used instead of wet processing, where scraping, grinding and distressing techniques are used.
3. Eco friendly dyes:
Generally, chemical dyes are used in denim coloration. But nowadays dyes which are being extracted from vegetable sources are also used as a colorant for denim fabric manufacturing. Natural indigo (Indigofera tinctoria) is grown in India and when it is used with environment-friendly reducing agents and alkali, the entire process becomes sustainable. This process is developed by SITRA which is now being used industry commercially.
4. Recycle of Denims:
Sweden has started this process, there near about 1500 tonnes of unused, wasted material have been recycled into new denims and 50 million litres of water have been saved.
5. Enzyme finish in denim washing:
It is the removal of surface dyes and protruding fibres to give the garment a rough appearance. Few years ago, pumice stones have been used to produce this effect. ‘acid wash’, ‘snow wash’, ‘whitewash’ and frosting, etc, are used as an alternative. Bio-degradable Cellulase enzymes are used as an alternative of stone wash to produce this effect.
6. Laser/dry treatment:
From its name we can understand that laser treatment is a dry technique where carbon dioxide gas is being used, laser is a source of energy computer-controlled laser beams are used to change the surface colour on denim fabrics. The laser beams are projected at a desired wavelength and intensity.
7. Ozone bleaching:
Ozone has strong oxidizing nature which can deteriorates indigo dyes on the fabric’s surface, producing a bleached look. Denim fabrics are being damped and exposed to the ozone for the treatment, and the desired bleaching level can be achieved in around 15 -20 minutes. Dry ozone techniques are also available, reduces the need for bleach and water, to create sustainable denim.
Related post: 17 Fashion Brands Sign up to The Jeans Redesign
Nowadays 100% organic cotton are being used without even bleaching of that cotton fabric where environment friendly enzyme finish and dry techniques are been used.
2. Dry techniques of denim manufacturing:
The dry technique of denim manufacturing is the process used instead of wet processing, where scraping, grinding and distressing techniques are used.
3. Eco friendly dyes:
Generally, chemical dyes are used in denim coloration. But nowadays dyes which are being extracted from vegetable sources are also used as a colorant for denim fabric manufacturing. Natural indigo (Indigofera tinctoria) is grown in India and when it is used with environment-friendly reducing agents and alkali, the entire process becomes sustainable. This process is developed by SITRA which is now being used industry commercially.
4. Recycle of Denims:
Sweden has started this process, there near about 1500 tonnes of unused, wasted material have been recycled into new denims and 50 million litres of water have been saved.
5. Enzyme finish in denim washing:
It is the removal of surface dyes and protruding fibres to give the garment a rough appearance. Few years ago, pumice stones have been used to produce this effect. ‘acid wash’, ‘snow wash’, ‘whitewash’ and frosting, etc, are used as an alternative. Bio-degradable Cellulase enzymes are used as an alternative of stone wash to produce this effect.
6. Laser/dry treatment:
From its name we can understand that laser treatment is a dry technique where carbon dioxide gas is being used, laser is a source of energy computer-controlled laser beams are used to change the surface colour on denim fabrics. The laser beams are projected at a desired wavelength and intensity.
7. Ozone bleaching:
Ozone has strong oxidizing nature which can deteriorates indigo dyes on the fabric’s surface, producing a bleached look. Denim fabrics are being damped and exposed to the ozone for the treatment, and the desired bleaching level can be achieved in around 15 -20 minutes. Dry ozone techniques are also available, reduces the need for bleach and water, to create sustainable denim.
Denim Brands and their initiatives in making denim jeans sustainable product
You know the top international player and their jeans brands. Here are few of them.- Levis
- Tommy Hilfiger
- Uniclo-Japan
- Wrangler
- Flying Machine
Related post: 17 Fashion Brands Sign up to The Jeans Redesign
The initiative taken to make denim fabric and jeans manufacturing supply chain more sustainable
LEVIS:
Levis started “WaterLess® innovations’’ in 2011. They have saved more than 3.5 billion litres of water in the finishing area of denim manufacturing as well as recycled over 5 billion more. Instead of washing a denim with fabric softener to create that worn-in feel, they have tumbled jeans with bottle caps and golf balls, taking the water out of the wash altogether — and saving 96% of it during the finishing process.2025 Water action strategy:
- Reducing water usage for manufacturing in high-stress areas by 50%.
- 80% of their factories and fabric mills will become distinguished ‘’Water<Less®’’ facilities — which means they will have water-saving guidelines.
Tommy Hilfiger:
Tommy Hilfiger has produced the 100% recycled cotton Spring 2019 TOMMY JEANS styles, from the leftover cotton which they generally procured from waste remnants cut components from cutting tables and factory floors and recycled using an innovative, entirely mechanical process that uses less water and lesser chemicals, reduces waste and generates less carbon footprint. Until now, creating a completely recycled cotton yarn, at scale, to the Tommy Hilfiger quality standard was hardly achievable.The sewing thread used is made from 100% recycled pet bottles, unused buttons stored in inventories from previous seasons, and the hangtags made from recycled paper. Each denim style has gone its finishing procedure using less water and energy by employing innovative laser technology to apply the final wash.
Tommy Hilfiger’s The Denim Lab is designed as a test centre for cutting-edge and sustainable finishing techniques. This includes ozone technology, which reduces water and chemical consumption by up to 70%, and laser machines that reduce the need for hand-scrapping and support the creation of denim finishes unique to the TOMMY HILFIGER brand.
Target by 2030: Fully circular products – all the materials we use to be part of a sustainable loop.
Target by the end of 2020: Procure 100% of our cotton from more sustainable sources
UNICLO:
The Jeans Innovation Center (JIC), stated their collaboration with UNICLO in November 2016 for the Fall/Winter 2019 season. The JIC introduces four technologies that will reduce water waste, time, and manual labor - The Laser Engraving System, the Nano-Bubble, the Ozone Washing, and the Water Recycling System.They are producing over 18 million pairs of jeans in this collaboration which reduces water by at least 90 percent compared to traditional methods
The Laser Engraving System is designed to create 60 jeans per hour as opposed to the 10 per hour it would take to distress jeans manually. Instead of stone washing Nano-Bubble is used , which also uses artificial EcoStone’s made of polymer to reduce waste. This new process uses up to 99 percent less water than the standard wash system. UNICLO uses Ozone Washing technology, which washes the denim without using water. As a result, jeans achieve a bleached, distressed way without the use of bleach. With its Water Recycling System, the water is used to go through recycling technology for purification, before being used once again to repeat the process.
Uniclo’s Target:
Their aim is to use 100 percent sustainable cotton in all its clothing by 2025, as well as to reduce its plastic use by 85 percent by 2020 — including using methods to minimize packaging waste.
WRANGLER:
Denim brand, Wrangler, has started the first denim apparel dyed with foam—Indigood, the latest technology that uses 100 percent less water than conventionally-dyed denim. The new dyeing process also reduces energy use and waste by more than 60 percent compared to the traditional denim dyeing process.Wranler’s Target:
They have said that
- they have conserving 5.5 billion litres of water at owned and operated facilities by the end of 2020
- using 100 percent preferred chemistry throughout its supply chain by end of 2020
- powering all owned and operated facilities with 100 percent renewable electricity by 2025 and
- sourcing 100 percent sustainable cotton by 2025.
FLYING MACHINE:
Brand from Arvind group has shown a 52% increase in the numbers of BCI cotton enabled farmers between mid-years of last decades. It also highlights that 5-year comprehensive plan to drive BCI ahead and develop Organic Cotton seeds. For their denim and its related production.They have saved Over 3 million kWh saving through introduction of energy saving led lamps at Santej, first Indian company to get certification in the Composite Textile Industry-denim fabric category, 11.78% decrease in GHG emissions at Naroda. Near about an 18% decrease in freshwater consumption at Naroda, 100% process water requirement sourced through treated municipal wastewater at Bangalore, 800kl/day of sewage water is treated and recycled every day. They are managing hazardous chemical spills, Salt- Recovery through Zero liquid discharge system, manufacturing easy wash fabrics for reducing the use of detergent and chemicals at the consumer end.
Beside this Lee continues to carry forward their dry techniques in denim manufacturing which requires no water and significantly fewer chemicals. In February, Mango launched a line of denim made from sustainable cotton with some styles washed using water minimizing technology from Jeanologia. Jack & Jones are using recycled materials from production leftovers.
References
https://organiccottonplus.com/pages/learning-center#questions-and-answers
https://www.cottonworks.com/topics/sourcing-manufacturing/denim/sustainable-denim-finishing/
https://kohantextilejournal.com/sitra-develops-100-green-technology-denims/
https://www.newindianexpress.com/magazine/2019/nov/17/wrangler-denims-sustainably-hip-2062596.html
https://www.businessoffashion.com/articles/news-analysis/wrangler-jeans-are-headed-to-china
https://www.fibre2fashion.com/
https://fashionunited.uk/
https://www.sgs.com/en/news/2019/07/more-sustainable-denim-production
https://www.drapersonline.com/insight/analysis/how-uniqlo-is-going-green-with-its-jeans
https://www.circle-economy.com/news/the-future-of-denim
https://www.textilesphere.com/2020/06/arvind-textile-limited-case-study.html
https://www.arvind.com/sustainability
References
https://organiccottonplus.com/pages/learning-center#questions-and-answers
https://www.cottonworks.com/topics/sourcing-manufacturing/denim/sustainable-denim-finishing/
https://kohantextilejournal.com/sitra-develops-100-green-technology-denims/
https://www.newindianexpress.com/magazine/2019/nov/17/wrangler-denims-sustainably-hip-2062596.html
https://www.businessoffashion.com/articles/news-analysis/wrangler-jeans-are-headed-to-china
https://www.fibre2fashion.com/
https://fashionunited.uk/
https://www.sgs.com/en/news/2019/07/more-sustainable-denim-production
https://www.drapersonline.com/insight/analysis/how-uniqlo-is-going-green-with-its-jeans
https://www.circle-economy.com/news/the-future-of-denim
https://www.textilesphere.com/2020/06/arvind-textile-limited-case-study.html
https://www.arvind.com/sustainability